材料“黑金”碳纤维:行业壁垒高,产品附加值大
一
碳纤维刚柔并济
下游应用广泛
材料发展史与人类发展史紧密相连,而新材料更是推动人类从“自然王国”走向“自由王国”的强大动力。材料通常被定义为用来制作有用物件的物质,人类对材料的认知和利用能力直接决定了社会形态与人类生活水平。在当代,材料、能源和信息已经成为构成社会文明和国民经济的三大支柱,而其中材料更是科学技术发展的物质基础和技术先导。
纵观整个材料发展史,以时间为维度可将其归纳为石器/青铜器/铁器/钢铁/硅/新材料这六个发展时期。其中,随着 20 世纪下半叶新技术革命的开启,新材料已然成为各高新技术领域发展的助推器,例如计算机技术依赖于半导体材料的工业化生产,宇航工业则需要大量高温高强度结构材料与之配套,而现代光纤通信更是以低消耗的光导纤维为基石。
◼ 抗疲劳能力强:碳纤维结构稳定,据高分子网统计,其复合材料经应力疲劳数百万次循环试验后,强度保留率仍有 60%,而钢材为 40%,铝材为 30%,玻璃钢则只有 20%-25%。
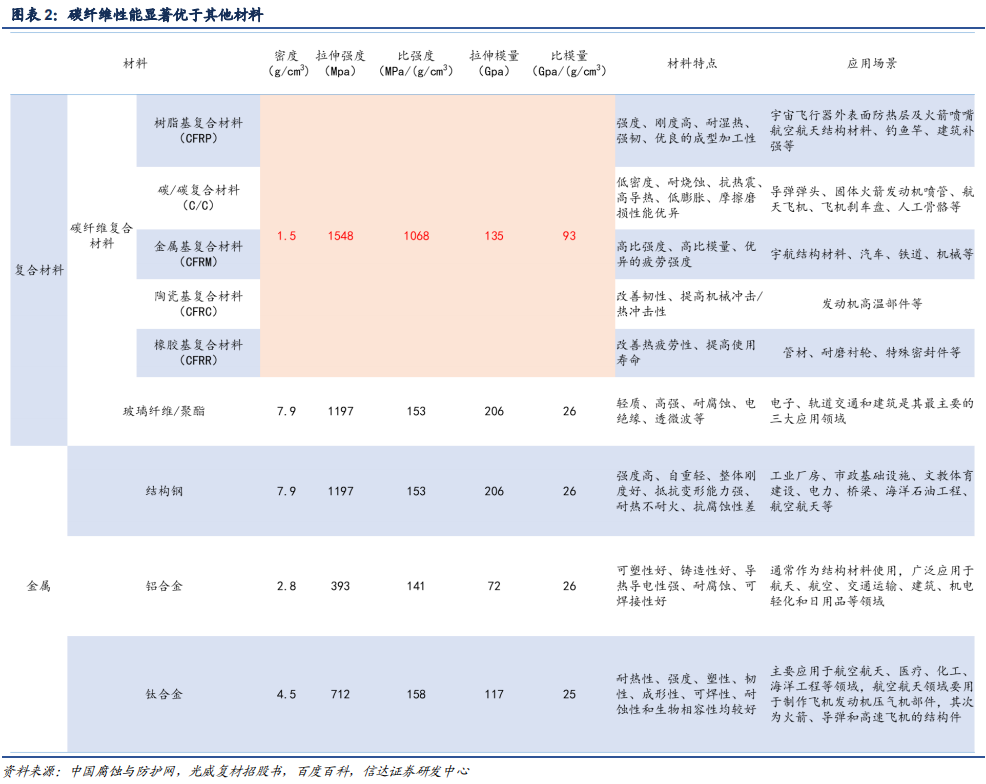
◼ 按原丝类型分类:聚丙烯腈(PAN)基、沥青基(各向同性、中间相);粘胶基(纤维素基、人造丝基)。其中,聚丙烯腈(PAN)基碳纤维占据主流地位,产量占碳纤维总量的 90%以上,粘胶基碳纤维还不足 1%。
◼ 按照制造条件和方法分类:碳纤维(800-1600℃)、石墨纤维(2000-3000℃)、活性碳纤维、气相生长碳纤维。
◼ 按力学性能可分为通用型和高性能型:通用型碳纤维强度在 1000MPa、模量在 100GPa 左右;高性能型又分为高强型(强度 2000MPa、模量 250GPa)和高模型(模量 300GPa 以上),其中强度大于 4000MPa 的又称为超高强型,模量大于 450GPa 的称为超高模型。
◼ 按丝束大小可分为小丝束和大丝束:小丝束碳纤维初期以 1K、3K、6K 为主,逐渐发展为 12K 和 24K,主要应用于航空航天、体育休闲等领域。通常将 48K 以上碳纤维称为大丝束碳纤维,包括 48K、60K、80K 等,主要应用于工业领域。
二
高壁垒带来高附加值
提升工艺、实现批量化生产
可显著降本增效
原丝生产是核心,碳化氧化是关键
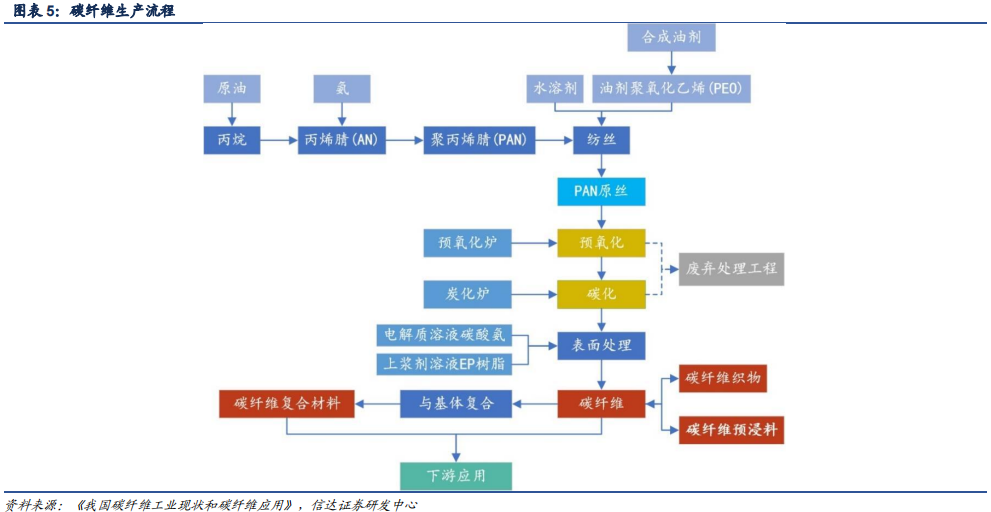
◼ 从原油中制得丙烷后,丙烷经选择性催化脱氢(PDH)可得到丙烯;
◼ 丙烯经氨氧化后得到丙烯腈,丙烯腈聚合和纺丝之后得到聚丙烯腈(PAN)原丝;
◼ 聚丙烯腈经过预氧化、低温和高温碳化后得到碳纤维,并可制成碳纤维织物和碳纤维预浸料,用于生产碳纤维复合材料;
◼ 碳纤维经与树脂、陶瓷等材料结合,形成碳纤维复合材料,最后由各种成型工艺得到下游应用需要的最终产品;

原丝质量、性能水平直接决定了碳纤维的最终性能。因此,提高纺丝液的质量,优化原丝成型的各项因素成为制备高品质碳纤维的关键节点。
据《聚丙烯腈基碳纤维原丝生产工艺研究》描述,纺丝工艺主要包括三大类:湿法纺丝、干法纺丝和干湿法纺丝。目前,国内外生产聚丙烯腈原丝的工艺主要采用湿法纺丝和干湿法纺丝,其中湿法纺丝的应用最为广泛。
湿法纺丝首先将纺丝液从喷丝孔挤出,纺丝液以细流的形态进入到凝固浴中。聚丙烯腈纺丝液的成丝机理是:纺丝液中与凝固浴中 DMSO(二甲基亚砜)的浓度存在较大差距,而凝固浴和聚丙烯腈溶液中水的浓度也存在巨大差距。在以上两种浓度差的相互作用下,液体之间开始双向扩散,通过传质、传热、相平衡移动等过程最终凝结成原丝。
原丝生产中 DMSO 残余量、纤度、单丝强度,模量,伸长率、含油率、沸水收缩率成为影响原丝质量的关键因素。以 DMSO 残余量为例,其对原丝表观性状、截面状态、最终碳纤维产品的 CV 值等均有影响,DMSO 残余量越低,产品的性能越高。生产中主要通过水洗的方式去除 DMSO,因而如何控制水洗温度、时间、脱盐水用量和水洗循量等因素就成为重要的环节。
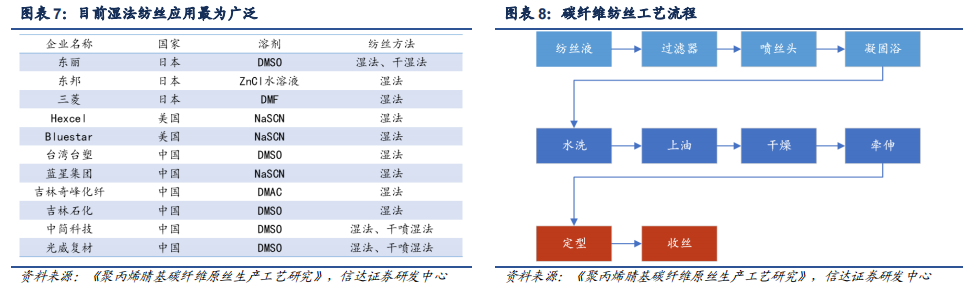
◼ 预氧化(200-300℃):预氧化环节通过在氧化性气氛中施加一定张力,对 PAN 原丝进行缓慢温和的氧化,在PAN 直链的基础上形成大量环装结构,从而达到可以耐受更高温度处理的目的。
◼ 碳化(最高温度不低于 1000℃):碳化过程需在惰性气氛中进行。碳化初期 PAN 直链断裂,开始进行交联反应;随着温度逐渐上升,热分解反应开始,释放出大量小分子气体,石墨结构开始形成;温度进一步上升后,碳元素含量迅速提高,碳纤维开始成型。
高技术壁垒赋予下游产品高附加值,航空复材价格较原丝翻 200 倍。由于碳纤维制备难度高,工艺复杂,因此其产品越往下游附加值越高,尤其是应用于航空航天领域的高端碳纤维复材,因下游客户对其可靠性、稳定性要求十分严苛,产品价格也较普通碳纤维呈几何倍数增长。
提高工艺、批量化生产均为降本良策
碳纤维生产成本较高,是新兴材料,更是“贵族”材料。可设计性较强的碳纤维属于新兴材料,但较高的原丝生产成本、环保投入及生产运输费用为其贴上了“贵族材料”的标签。据《碳纤维产业化发展及成本分析》论述,较高质量的 PAN 原丝投入与碳纤维产出比约 2.2:1,较低质量的原丝与碳纤维产出比约 2.5:1,叠加聚合、喷丝、碳化氧化等过程对环境、综合技术等要求较高,进一步导致碳纤维生产成本居高不下。
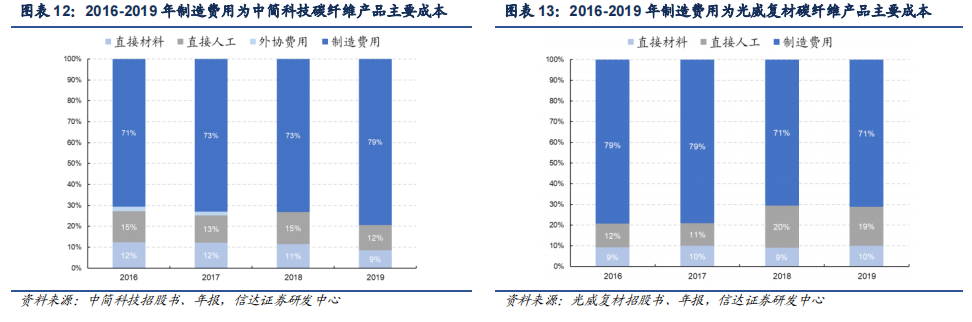
以生产流程为维度,聚合、纺丝和碳化氧化是其生产成本的主要构成:
◼ 聚合:该阶段主要包括由原料和生产物资消耗构成的直接生产成本、由纯化与输送原料、聚合、过滤/输送原液、回收单体/溶剂等成本构成的生产过程成本,以及由蒸汽、电力、水、配套设施运维等成本构成的综合生产成本。
◼ 纺丝:生产成本集中在过滤/ 输送聚合液、纺丝、净化等。产业链中,原丝一般在碳纤维成本中占比 51%。
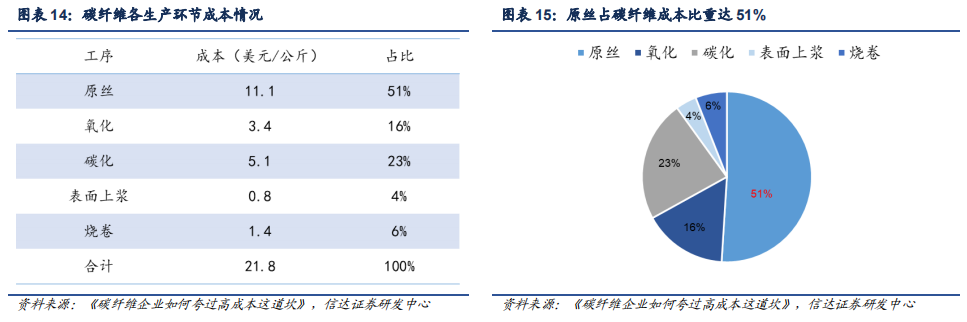
提高纺丝、碳化氧化等环节工艺可显著降低成本。具体方法包括:
提升产量可带来规模效应,有效降低碳纤维生产成本。据《碳纤维产业化发展及成本分析》统计,原丝和碳纤维的产能和生产成本呈反比关系。随着产能的扩大,原丝和碳纤维产线直接生产成本的增幅显著小于单耗成本、固定资产折旧和流动费用等成本的降幅,千吨级碳纤维产线每年成本较百吨级产线下降 18%。
三
我国碳纤维产业方兴未艾
潜力巨大
技术创新助推碳纤维性能提升,国产化替代是行业不变“旋律”。我国自 20 世纪 60 年代后期便开始 PAN 基碳纤维研究,历经半个世纪发展,现阶段虽仍与国外有显著差距但已可自主制备以 T700、T800、M55J 等为代表的一系列高端碳纤维,成功打破国外的技术封锁,成绩斐然。
纵观国内碳纤维发展史,我们将其归纳为以下五个阶段:
◼ 举国体制,从无到有(1962-1982):该阶段我国碳纤维研究刚起步,国家高度重视碳纤维研发工作,PAN 基碳纤维研制课题组、高分子复合材料物理研究室相继成立,建成 PAN 原丝试制能力约 50 吨/年,碳纤维长丝试制能力 1.5-2.0 吨/年,解决了碳纤维从无到有的问题。
◼ 尝试引进,于困难中摸索(1983-1990):该时期国家科委鼓励引进国外先进技术并承诺将给予资金支持,但由于碳纤维技术涉及国防等领域,叠加“巴黎统筹条约”的限制,引进过程举步维艰,经多次谈判考察,我国最终以 450 万美元从英国 RK 公司购入生产能力 100 吨(12K) /年的碳化设备,但运行效率较低。
◼ “停滞”的十年(1990-2000):由于碳纤维生产的复杂性和国外对我国的技术封锁,国家虽积极组织各研究单位合力攻关但关键技术依旧难以突破,该时期只有吉化公司、吉林碳素厂和北京化工学院在维持小批量供货,其他研发单位陆续退出该领域。
◼ “大干快上”,碳纤维迎来建设浪潮(2000-2010):在师昌绪院士的动员和国家大力支持下,科技部决定设立碳纤维专项,并成立专家组,将碳纤维列入 863 计划新材料领域。此外,大量民间资本的涌入也催生出一批碳纤维生产企业,据《2019 全球碳纤维复合材料市场报告》统计,2000-2010 年,拥有碳纤维项目的科研院所和生产单位达 40 家以上,投资规模超过 300 亿元,全世界碳纤维设备制造厂也迎来了中国盛宴。
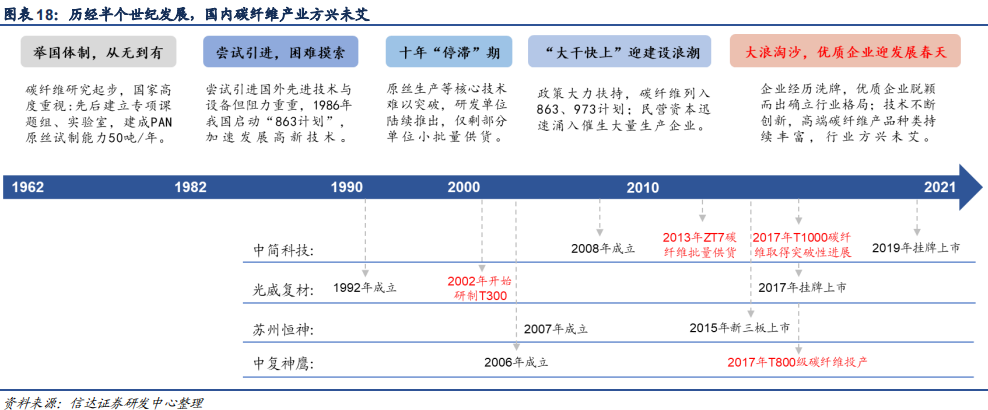
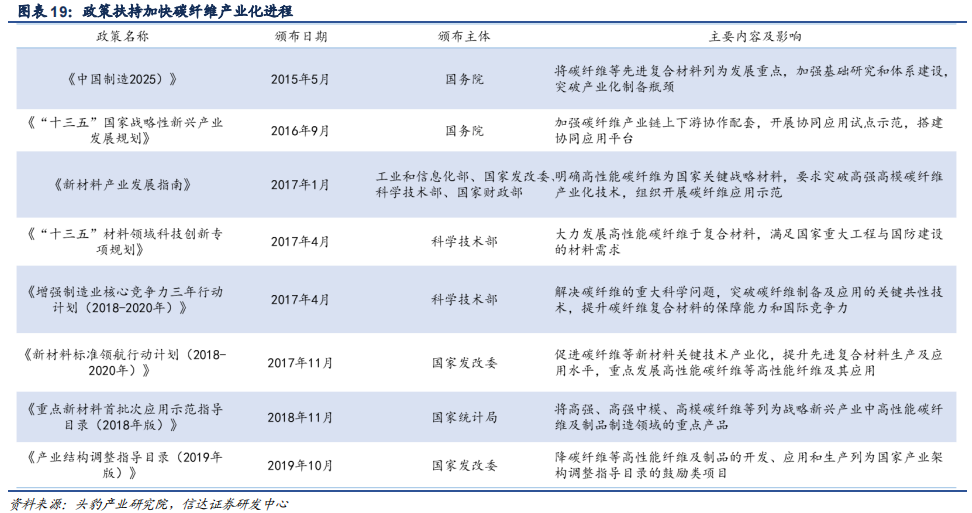
报告来源 | 信达证券
本文有删减,全文详见报告原文